The Advantages of Partnering with a Custom CNC Parts Manufacturer
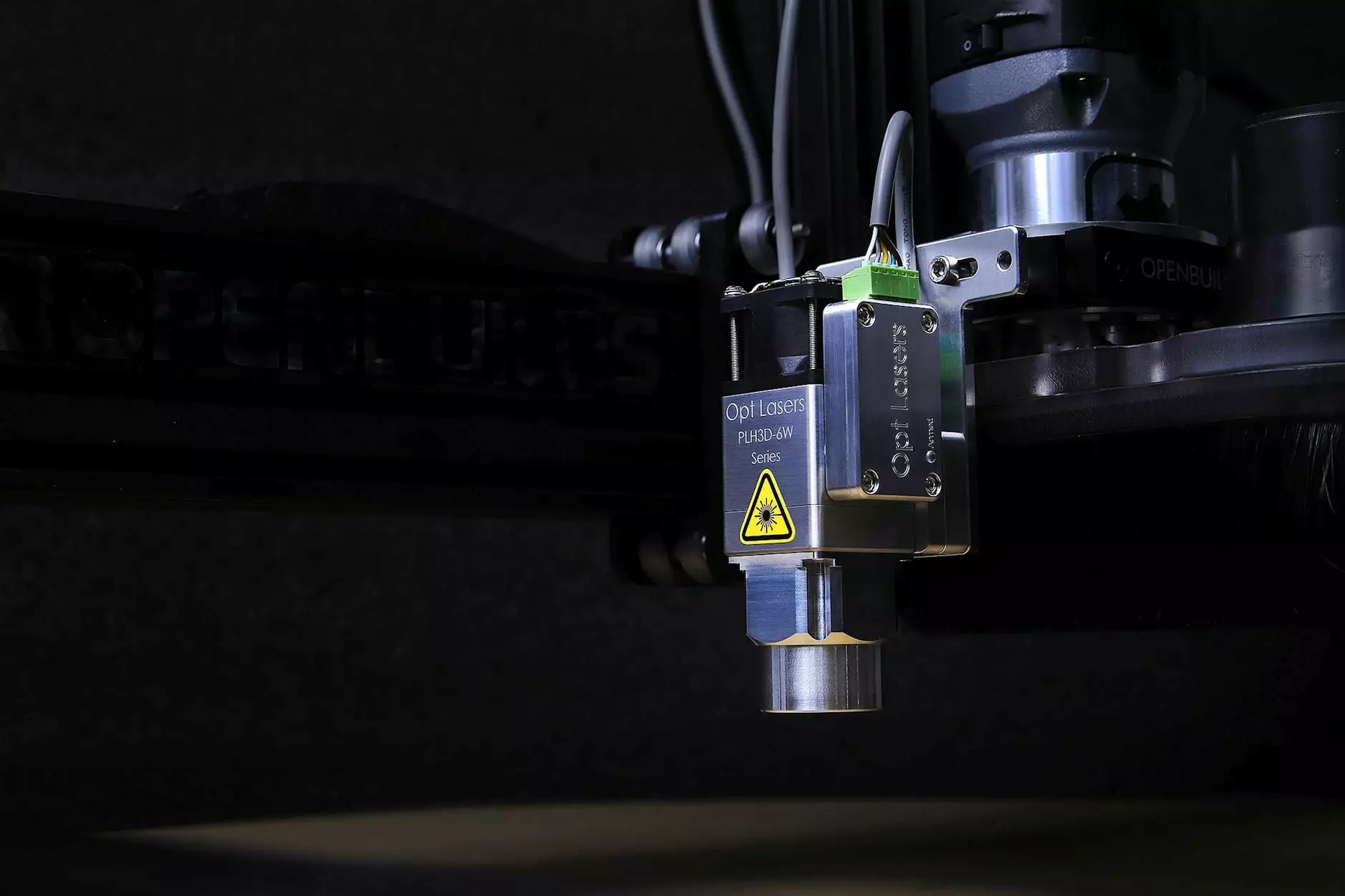
Custom CNC parts manufacturing is revolutionizing the way businesses operate in various industries. Today's manufacturing processes require precision, flexibility, and quality, and CNC (Computer Numerical Control) machining delivers all of these components effectively. This article will delve into why choosing a reliable custom CNC parts manufacturer like DeepMould.net can significantly enhance your production capabilities.
Understanding CNC Machining
CNC machining is a modern manufacturing method that utilizes computer programming to control machining tools. This method enables manufacturers to create high-precision components with intricate designs and complex geometries. Armed with advanced technology, a custom CNC parts manufacturer can produce items with minimal human intervention, reducing error rates while increasing output consistency.
The Technology Behind CNC Machining
The core of CNC machining involves the use of computer-aided design (CAD) and computer-aided manufacturing (CAM). Here's how this technology works:
- Design Creation: Engineers create a detailed CAD model of the part, specifying its dimensions, tolerances, and surface finishes.
- Program Generation: The CAD model is converted into a CAM program that dictates how the CNC machine should perform.
- Machining Process: The CNC machine follows the programmed instructions to cut, shape, and finish the materials into the desired component.
Benefits of Working with Custom CNC Parts Manufacturers
1. Precision and Accuracy
One of the most significant advantages of teaming up with a custom CNC parts manufacturer is the ability to produce parts with remarkable precision. CNC machines can achieve tolerances of ±0.001 inches or even tighter, depending on the material and complexity of the design. This level of accuracy is vital in industries such as aerospace, automotive, and medical, where even the slightest imperfections can lead to major failures.
2. Flexibility in Design
Custom CNC machining allows for a high degree of design flexibility. Manufacturers can produce parts in various shapes and sizes, accommodating unique specifications and requirements. This flexibility is particularly beneficial for industries that are often faced with custom orders or need to rapidly adjust designs based on market demands.
3. Material Variety
Another considerable benefit is the vast selection of materials that can be machined. From metals like aluminum and stainless steel to plastics and composites, a custom CNC parts manufacturer can work with various materials tailored to your project's specific needs. This capability ensures that companies can select the proper material to enhance durability, reduce weight, or optimize cost.
4. Increased Production Efficiency
Utilizing CNC machines can dramatically streamline the manufacturing process. Unlike traditional machining, which can be more time-consuming and labor-intensive, CNC processes are automated and can run continuously, often producing parts much faster. This efficiency not only helps meet tight deadlines but also reduces labor costs significantly.
The Role of DeepMould.net in the CNC Manufacturing Space
As a leading custom CNC parts manufacturer, DeepMould.net stands out in its commitment to quality, precision, and customer service. Here are several factors that set DeepMould.net apart:
Expert Team of Engineers
Our team comprises highly skilled engineers and technicians who understands the intricacies of CNC machining. Our expertise ensures that every part manufactured meets the highest industry standards, providing peace of mind to our clients.
State-of-the-Art Equipment
At DeepMould.net, we utilize the latest CNC machinery available on the market. Our investment in technology allows us to produce intricate designs and complex parts with immaculate accuracy. From 3D printing to multi-axis CNC machines, we have the equipment to handle any project.
Quality Assurance Processes
Quality is our utmost priority. We employ rigorous quality control measures, including comprehensive inspections throughout the manufacturing process. All parts undergo detailed checks against our clients' specifications to guarantee that they meet the required standards before delivery.
Applications of Custom CNC Parts Manufacturing
The applications for custom CNC parts are vast and varied. Industries that benefit significantly from this manufacturing method include:
- Aerospace: Precision components for aircraft and spacecraft systems.
- Automotive: Custom parts such as brackets, engine components, and interior fittings.
- Medical: Parts for surgical instruments, medical devices, and implants.
- Energy: Custom fixtures and components for renewable energy systems.
- Electronics: Enclosures and mounts for various electronic devices.
Selecting the Right Custom CNC Parts Manufacturer
1. Define Your Needs
Before approaching a custom CNC parts manufacturer, businesses should clearly define their needs. Consider factors such as production volume, tolerances, material types, and finish requirements.
2. Research and Compare Manufacturers
Take the time to research potential manufacturers. Look for experience in your industry, read customer reviews, and inquire about their capabilities. Comparing quotes and lead times can also provide valuable insight into which manufacturer best suits your project.
3. Check Certifications and Quality Standards
Ensure that the manufacturer adheres to relevant industry standards (such as ISO certifications) to guarantee quality and reliability in their processes.
Conclusion
In today's competitive landscape, leveraging the expertise of a custom CNC parts manufacturer like DeepMould.net can provide businesses with significant advantages. From unmatched precision and material versatility to enhanced operational efficiency, the benefits are clear. Partnering with experts in the field not only simplifies the manufacturing process but enables businesses to focus on growth and innovation.
For your next project, consider incorporating the numerous benefits that custom CNC machining has to offer. Experience the difference of working with a trusted manufacturer that prioritizes quality, precision, and customer satisfaction.