Understanding Positive Displacement Pumps: A Comprehensive Guide
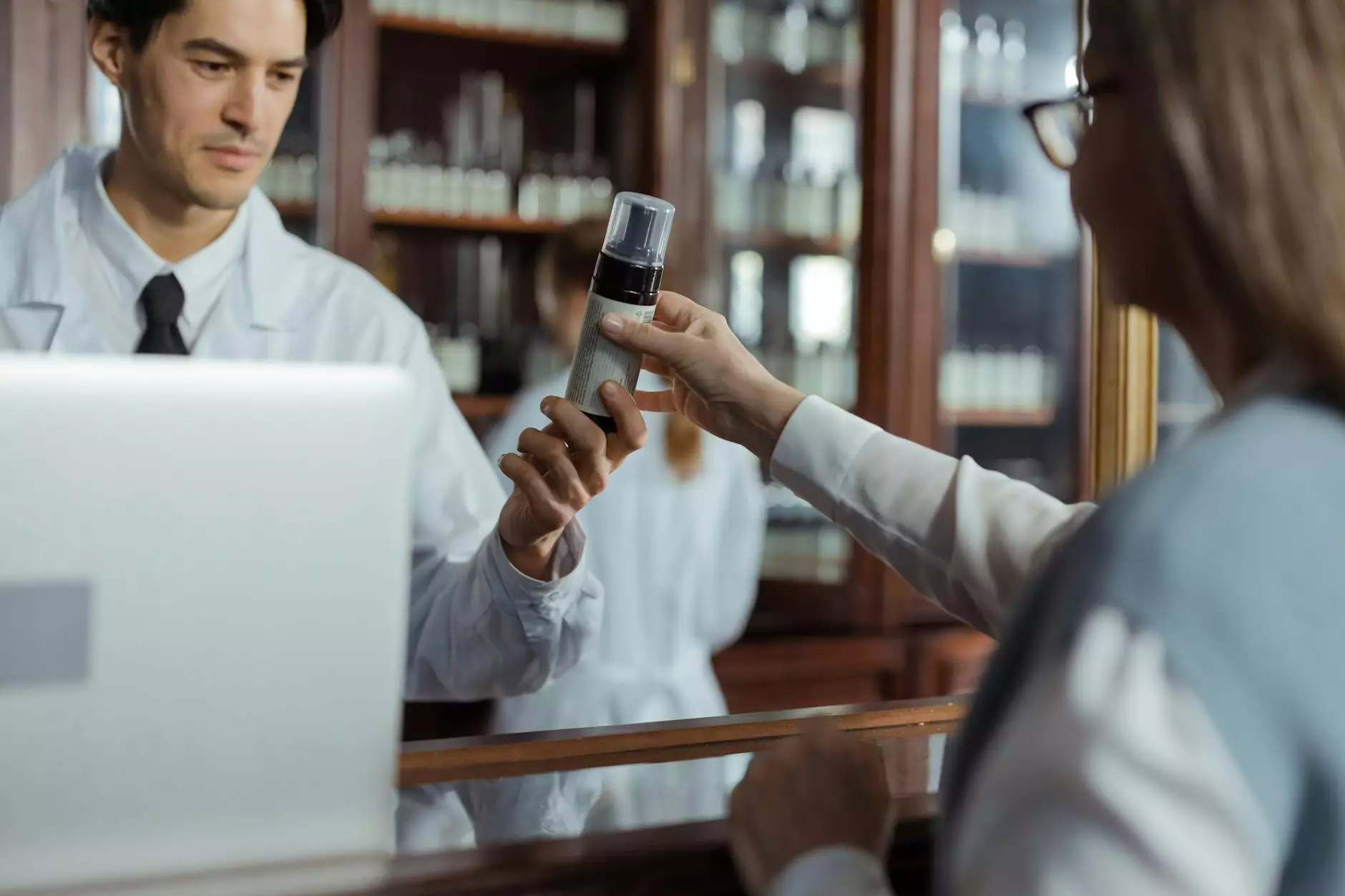
Positive displacement pumps are vital components in various industrial applications due to their unique operating principles and capabilities. This article aims to explore in-depth the intricacies of positive displacement pumps, their advantages, and their applications across different sectors, including auto repair, farm equipment repair, and structural engineering.
What is a Positive Displacement Pump?
A positive displacement pump is a type of pump that moves fluid by trapping a fixed amount of it and forcing that trapped volume into the discharge pipe. Unlike centrifugal pumps, which use rotational energy to move liquid, positive displacement pumps rely on the direct displacement of fluid through mechanical means. This makes them incredibly effective for a variety of applications.
How Does a Positive Displacement Pump Work?
The mechanism of a positive displacement pump can be broken down into several key components:
- Chamber: This is where the initial operation occurs, trapping the fluid to be pumped.
- Valves: They ensure that fluid flows in one direction, preventing backflow.
- Drive Mechanism: This can be manual or motorized. It facilitates the movement of the displaced fluid.
The operation sequence typically involves the following steps:
- The pump's chamber fills with fluid.
- Once filled, the pump mechanism forces the fluid out against the resistance of the system.
- The cycle continues, allowing for a constant and steady flow of fluid.
Types of Positive Displacement Pumps
There are two primary types of positive displacement pumps commonly used in various industries:
1. Gear Pumps
Gear pumps utilize rotating gears to create a vacuum that pulls in fluid.
- Applications: Gear pumps are widely used in automotive applications for circulating oil and fuel.
- Advantages: They are compact, efficient, and can handle high-viscosity fluids.
2. Diaphragm Pumps
Diaphragm pumps use a flexible membrane to move fluid in and out of the pumping chamber.
- Applications: Commonly used in chemical processing, they are suitable for handling corrosive fluids.
- Advantages: They are self-priming and can run dry without damage.
Benefits of Using Positive Displacement Pumps
Choosing a positive displacement pump comes with numerous advantages that make them an excellent choice for various applications:
- Consistent Flow Rate: Unlike centrifugal pumps that fluctuate based on system pressure, positive displacement pumps maintain a constant flow rate irrespective of discharge pressure.
- Versatility: They can handle a wide range of fluids, including viscous and thixotropic substances.
- Self-Priming Capability: Most designs offer self-priming, making them easy to operate without the need for additional equipment.
- Durability: Built to withstand harsh conditions, many positive displacement pumps can operate in extreme temperatures and pressures, enhancing their lifespan.
Applications of Positive Displacement Pumps
Positive displacement pumps find applications across various industries:
Auto Repair
In the auto repair industry, positive displacement pumps are essential for:
- Fuel injection systems
- Engine oil circulation
- Power steering fluid management
These pumps provide reliable and efficient performance in circulating various automotive fluids, ensuring optimal engine function.
Farm Equipment Repair
Farm equipment often requires robust and reliable pumping solutions. Positive displacement pumps are used for:
- Fertilizer application
- Irrigation systems
- Crop spray systems
Their ability to deliver accurate flow rates is critical in agricultural settings, promoting healthy crop production.
Structural Engineering
In structural engineering, these pumps are invaluable for:
- Pumping concrete and other fluids during construction projects
- Managing slurry in excavation sites
- Water control in tunnels and basements
Positive displacement pumps ensure that construction activities proceed without interruption, enhancing productivity.
Factors to Consider When Selecting a Positive Displacement Pump
When choosing a positive displacement pump for your specific needs, consider the following factors:
- Fluid Characteristics: Understand the viscosity and chemical composition of the fluid you'll be pumping.
- Flow Rate: Determine the required flow rate for your application to ensure the pump meets those demands.
- Pressure Requirements: Assess the discharge pressure needed to effectively complete your tasks.
- Operational Environment: Consider the environmental conditions the pump will operate in, such as temperature and exposure to chemicals.
Maintenance Tips for Positive Displacement Pumps
Proper maintenance of positive displacement pumps is crucial for ensuring longevity and efficient operation:
- Regular Inspections: Routine checks can identify wear and tear early, preventing major breakdowns.
- Lubrication: Ensure all moving parts are adequately lubricated to minimize friction and wear.
- Monitor Performance: Keep track of flow rates and pressure to catch anomalies that may indicate issues.
- Cleaning: Regularly clean the pump and associated components to avoid clogging and contamination.
Conclusion
In summary, positive displacement pumps play an integral role across various industries, including automotive, agricultural, and engineering sectors. Their unique design, coupled with several operational advantages, makes them an ideal choice for many applications. By understanding the workings, benefits, and maintenance of these pumps, businesses can make informed choices, ensuring efficient operations and longevity of equipment. If you are looking for reliable solutions for your pumping needs, consider reaching out to professional service providers like Michael Smith Engineers, a trusted name in auto repair, farm equipment repair, and structural engineering.